Discover the factors that impact high and low hours on equipment in this comprehensive blog post. From idle hours and environmental conditions to previous applications and repair history, explore the key considerations for assessing equipment longevity. Make informed decisions and ensure reliable performance with a thorough understanding of these factors.
Introduction
When considering the purchase of used equipment, understanding the significance of high and low hours is crucial. However, assessing these hours should not be limited to numerical values alone. Several factors can influence the machine’s longevity, value, and overall condition. In this comprehensive blog post, we will delve deeper into the factors affecting high and low equipment hours, providing you with a thorough analysis to make informed decisions.
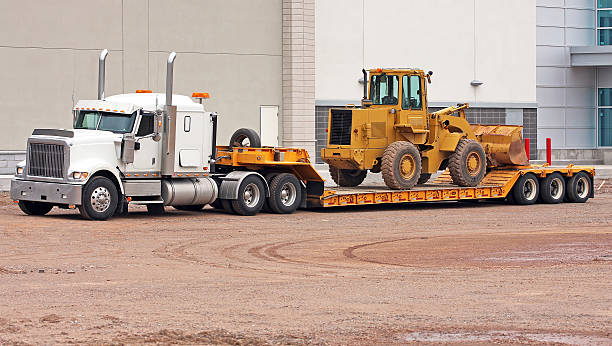
1. Idle Hours
Understanding the Impact Idle hours, referring to the time when the machine is running but not actively engaged in any operation, have varying implications depending on the equipment. While idle hours accumulate on the hour meter, the wear and tear during this period are generally minimal, except for the engine. Some wheel loaders even incorporate features that automatically increase engine RPM to maintain engine longevity while idling. By considering idle hours, you can gain insights into the equipment’s overall usage and potential lifespan.
2. Environmental Conditions
From Heat to Cold The environment in which the equipment operates significantly affects its performance and durability. High-temperature environments, for example, can pose risks to components such as seals, O-rings, gaskets, and turbos. Heat can accelerate the degradation of these parts, reducing their lifespan. On the other hand, cold environments present their challenges. Hydraulic systems, particularly in cold weather, may suffer from increased wear and tear due to thickening hydraulic oil, potentially leading to cylinder and seal damage. Understanding the environmental conditions, the equipment has been exposed to is vital for assessing its long-term reliability.
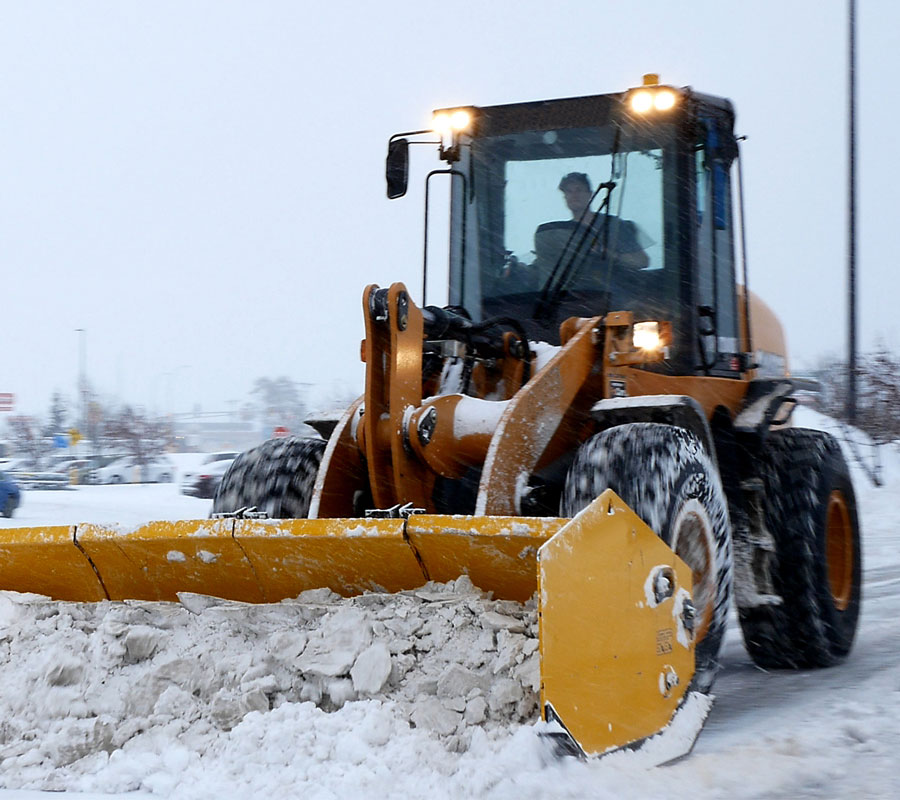
3. Previous Applications
Determining to Wear and Tear The application in which the equipment was previously used provides insights into the stress placed on its components. Whether it was involved in snow removal, industrial yard operations, pipe moving, general excavation, or agricultural activities, each application carries different levels of wear and tear. Specific jobs require more extensive use of the machine’s functions and impose higher stress on its components. Knowing the previous applications can help gauge the potential impact on the equipment’s overall condition.
4. Environmental Factors
The Role of Location The location where the equipment was previously used can significantly influence its condition and appearance. Coastal areas, for instance, with their high salt content in the air, accelerate rusting and corrosion, affecting various features and components of the machine. Rubber and hydraulic hoses, as well as the engine, are particularly susceptible to salt-related damage. Similarly, high humidity or dusty environments can affect seals and engine performance. Clean air is crucial for optimal engine operation. Understanding the environmental factors influencing the equipment’s condition is essential for an accurate assessment.
5. Repair and Maintenance History
Unveiling the Machine’s Care The repair and maintenance history of the equipment unveils its overall care and attention. Regular maintenance, following manufacturer guidelines, ensures proper upkeep and minimizes the risks of breakdowns. Access to maintenance records allows you to identify past replacements and repairs, offering a comprehensive understanding of the machine’s previous ownership and potential future maintenance requirements. Knowledge of the repair and maintenance history adds value to your decision-making process and helps determine the long-term reliability of the equipment.
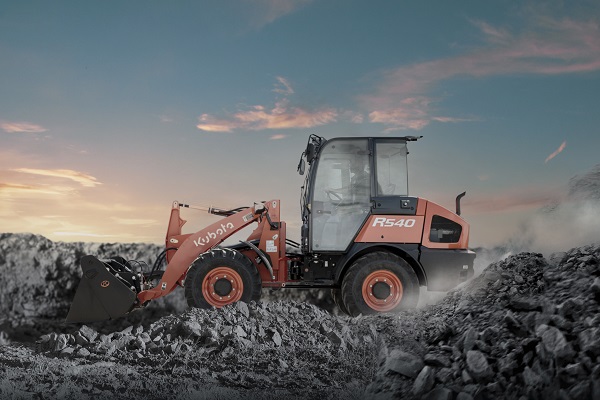
Conclusion:
Evaluating used equipment requires a comprehensive analysis of factors beyond high and low hours. Idle hours, environmental conditions, previous applications, environmental factors, and repair and maintenance history collectively contribute to assessing a machine’s longevity and value. By considering these factors, you can make an informed decision, ensuring the longevity, reliability, and performance of the equipment you invest in. Remember, proper maintenance and adherence to manufacturer guidelines are essential for maximizing the lifespan of your machinery.
For more detailed insights into equipment maintenance, be sure to explore our dedicated maintenance blog, where we delve deeper into essential repairs and maintenance practices to preserve the longevity of your equipment and minimize unexpected breakdowns. Equip yourself with knowledge and make well-informed decisions for your equipment investment journey.